El Instituto de Energía Solar Francesa Ines ha desarrollado nuevos módulos fotovoltaicos con termoplásticos y fibras naturales obtenidas en Europa, como el lino y el basalto. Los científicos apuntan a reducir la huella ambiental y el peso de los paneles solares, al tiempo que mejoran el reciclaje.
Un panel de vidrio reciclado en la parte delantera y un compuesto de lino en la parte posterior
Imagen: GD
De la revista PV Francia
Los investigadores del Instituto Nacional de Energía Solar de Francia (INES), una división de las energías alternativas francesas y la Comisión de Energía Atómica (CEA), están desarrollando módulos solares con nuevos materiales biológicos en los lados delanteros y traseros.
"A medida que la huella de carbono y el análisis del ciclo de vida se han convertido en criterios esenciales en la elección de los paneles fotovoltaicos, el abastecimiento de materiales se convertirá en un elemento crucial en Europa en los próximos años", dijo Anis Fouini, director de CEA-Lines , en una entrevista con la revista PV France.
Aude Derrier, coordinador del proyecto de investigación, dijo que sus colegas han analizado los diversos materiales que ya existen, para encontrar uno que pueda permitir a los fabricantes de módulos producir paneles que mejoren el rendimiento, la durabilidad y el costo, al tiempo que reducen el impacto ambiental. El primer demostrador consiste en células solares de heterounión (HTJ) integradas en un material totalmente compuesto.
"El lado frontal está hecho de un polímero lleno de fibra de vidrio, que proporciona transparencia", dijo Derrier. "El lado trasero está hecho de compuesto basado en termoplásticos en los que se ha integrado un tejido de dos fibras, lino y basalto, lo que proporcionará resistencia mecánica, pero también una mejor resistencia a la humedad".
El lino se obtiene del norte de Francia, donde todo el ecosistema industrial ya está presente. El basalto se obtiene en otra parte de Europa y es tejido por un socio industrial de Ines. Esto redujo la huella de carbono en 75 gramos de CO2 por vatio, en comparación con un módulo de referencia de la misma potencia. El peso también fue optimizado y es de menos de 5 kilogramos por metro cuadrado.
"Este módulo está dirigido al PV de la azotea y la integración del edificio", dijo Derrier. “La ventaja es que es naturalmente de color negro, sin la necesidad de una hoja de atrás. En términos de reciclaje, gracias a los termoplásticos, que se pueden recordar, la separación de las capas también es técnicamente más simple ”.
El módulo se puede hacer sin adaptar los procesos de corriente. Derrier dijo que la idea es transferir la tecnología a los fabricantes, sin inversiones adicionales.
"El único imperativo es tener congeladores para almacenar el material y no comenzar el proceso de reticulación de resina, pero la mayoría de los fabricantes de hoy usan Prepreg y ya están equipados para esto", dijo.
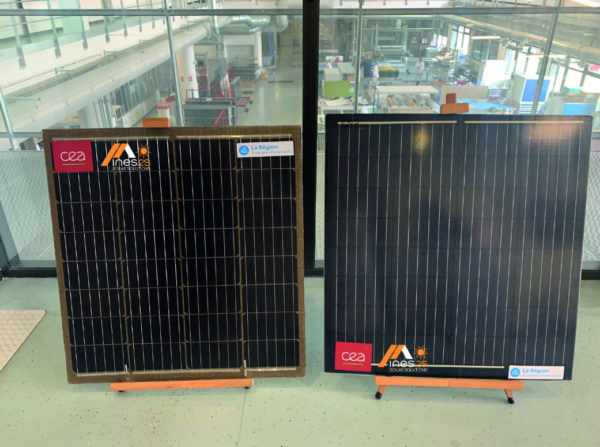
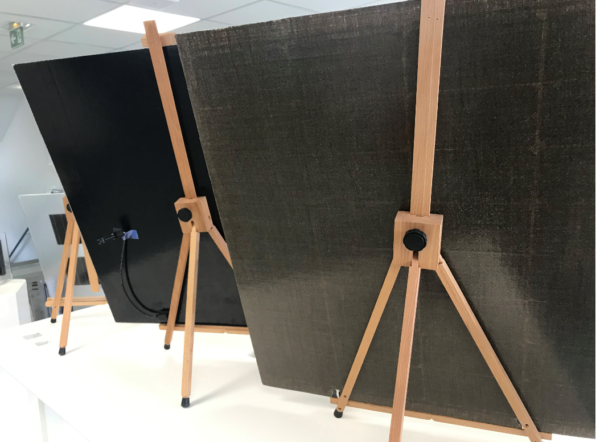
"Trabajamos en la segunda vida de vidrio y desarrollamos un módulo compuesto por vidrio reutilizado de 2.8 mm que proviene de un módulo antiguo", dijo Derrier. "También hemos utilizado un encapsulante termoplástico que no requiere reticulación, lo que, por lo tanto, será fácil de reciclar, y un compuesto termoplástico con fibra de lino para resistencia".
La cara trasera sin basalto del módulo tiene un color de lino natural, que podría ser estéticamente interesante para los arquitectos en términos de integración de fachadas, por ejemplo. Además, la herramienta de cálculo de INES mostró una reducción del 10% en la huella de carbono.
"Ahora es imperativo cuestionar las cadenas de suministro fotovoltaica", dijo Jouini. “Con la ayuda de la región Rhône-Alpes en el marco del Plan de Desarrollo Internacional, por lo tanto, buscamos jugadores fuera del sector solar para encontrar nuevos termoplásticos y nuevas fibras. También pensamos en el proceso de laminación actual, que es muy intensivo en energía ".
Entre la presurización, la fase de presión y de enfriamiento, la laminación generalmente dura entre 30 y 35 minutos, con una temperatura de funcionamiento de alrededor de 150 C a 160 C.
"Pero para los módulos que incorporan cada vez más materiales de diseño ecológico, es necesario transformar los termoplásticos a alrededor de 200 C a 250 C, sabiendo que la tecnología HTJ es sensible al calor y no debe exceder las 200 C", dijo Derrier.
El Instituto de Investigación se está asociando con el especialista en termocompresión de inducción con sede en Francia Roctool, para reducir los tiempos de ciclo y hacer formas de acuerdo con las necesidades de los clientes. Juntos, han desarrollado un módulo con una cara trasera hecha de compuesto termoplástico de tipo polipropileno, al que se han integrado fibras de carbono recicladas. La parte frontal está hecha de termoplásticos y fibra de vidrio.
"El proceso de termocompresión de inducción de Roctool hace posible calentar las dos placas delanteras y traseras rápidamente, sin tener que alcanzar 200 C en el núcleo de las células HTJ", dijo Derrier.
La compañía afirma que la inversión es menor y el proceso podría lograr un tiempo de ciclo de solo unos pocos minutos, mientras usa menos energía. La tecnología está dirigida a los fabricantes compuestos, para darles la posibilidad de producir partes de diferentes formas y tamaños, al tiempo que integran materiales más ligeros y duraderos.
Tiempo de publicación: Jun-24-2022